3.1 Straw treatment, transportation, and combustion An independent straw warehouse shall be built in the power plant, and the moisture content of straw shall be tested. Any package of straw with a moisture content exceeding 25% is considered unacceptable. In European power plants, this test is carried out using infrared sensors mounted on automatic cranes. In China, a detector can be manually inserted into each straw bale to test for moisture. The detector can store 99 sets of measured values. After measuring all straw bales, the measurement results can be stored in a computer connected to the weighbridge. Then use a forklift to unload and input the empty weight of the transport truck into the computer. The computer can calculate the net weight of the straw based on the weight before and after the straw and the water content.
When the truck is unloading, the forklift puts the straw bales into a predetermined position; At the other end of the warehouse, a forklift truck places the straw bales on the feed conveyor; The feed conveyor has a buffer table that can retain straw for 5 minutes; Straw is conveyed from the feed table to the feed system through a feed conveyor with a sealed gate (fire proof); The straw bales are pushed onto two vertical screws, which are rotated to break the straw, and then conveyed to a spiral automatic feeder, which presses the straw into a sealed feed channel, and then conveyed to the furnace bed. The furnace bed is a water cooled vibrating furnace, which is specially developed for straw burning power plants.
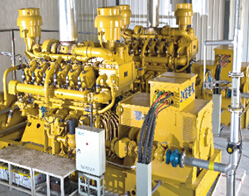
The boiler system adopts a naturally circulating drum boiler, with superheaters arranged in two stages in the flue, and economizers and air preheaters arranged at the tail of the flue. Due to the relatively high content of alkali metals in straw ash, flue gas is highly corrosive at high temperatures (above 450 ℃). In addition, the melting point of fly ash is low, which is prone to the problem of slagging. If ash becomes solid and semi fluid, it is difficult to remove during operation, and it will hinder the heat transfer from flue gas to steam in the pipeline. In severe cases, it may even completely block the flue gas passage, blocking the flue gas in the boiler. Due to these problems, a superheater system has been specially designed.
3.3 The steam turbine and boiler in the steam turbine system must be consistent in terms of startup, partial load, and shutdown operations. Coordination of the work of the boiler, steam turbine, and condenser is very important. 3.4 Environmental Protection System After the wet flue gas purification system, a bag filter is installed to collect the fly ash in the flue gas. The emissions from bag filters are less than 25 mg/Nm3, significantly lower than the level of soot emissions from coal-fired power plants in China.
3.5 The by-product straw usually contains 3% to 5% ash. This ash is collected in the form of boiler fly ash and ash/bottom ash, which is rich in nutrients such as potassium, magnesium, phosphorus, and calcium and can be used as efficient agricultural fertilizers.
For more questions or detailed information about gas turbine generators, please visit our company's website: There will be a lot of content on the website for reference only.