Technical requirements for gas magazines for gas internal combustion generator sets
The impact of solid particles such as dust on gas internal combustion generator sets mainly lies in causing filter blockage, insufficient air intake, and pressure reduction. Inside the engine cylinder, it can cause wear on the cylinder wall and piston, as well as contaminate the lubricating oil, resulting in wear on other components such as sliding bearings and affecting the normal operation of the unit. The built-in filter of the engine gas intake valve group is only used to protect the system from particle damage and cannot be used as a workload filter. Users should install a workload filter in the gas pipeline, and the filter should be installed when the particle diameter is greater than 3 μ At m, the separation rate must reach 99.99% or above.
For combustion air, Yanbach gas generator sets require that the particulate matter content in the air should not exceed 0.1 mg/Nm3, and the combustion air filter should at least meet the EN779 G3 level. It is necessary to ensure that the exhaust gases from various processes (such as industrial waste gas, biological process exhaust gas, or solvents) cannot enter the engine combustion air to avoid affecting engine operation.
sulfur
Gases such as biogas often contain sulfur containing compounds such as hydrogen sulfide. If burned in the cylinder, sulfur dioxide and sulfur trioxide are formed. Due to the presence of moisture in gas and the generation of moisture during combustion, sulfur-containing compounds dissolve in water to form hydrosulfuric acid, sulfite, and sulfuric acid, which can corrode engine metal components. Sulfur-containing compounds dissolved in engine oil can also acidify the oil, reduce its lubrication ability, shorten its service life, and have corrosive effects on components that need to be lubricated through oil in the engine, such as bearing shells, cam rocker mechanisms, etc. In addition, sulfur compounds can also corrode the metal electrodes of spark plugs, shortening their service life.
The specific requirements for gas sulfur content in gas internal combustion generator sets are related to the unit model and gas methane concentration. Generally, the total sulfur content in the gas entering the engine should be less than 300 mg/Nm3. In addition, models with pre combustion chambers typically have additional requirements. If there is a tail gas treatment equipment with a catalyst, it is also necessary to consider the catalyst's requirements for sulfur content.
In a cogeneration system, engine exhaust is often heat exchanged through a flue gas hot water heat exchanger to recover exhaust heat. If the flue gas temperature drops below the acid dew point of sulfur oxides (SOx), it will cause corrosion to the heat exchanger. Figure 1 shows the curve between the concentration of sulfur oxides and the acid dew point.
Volatile Organic Silicon Compounds (VOSC)
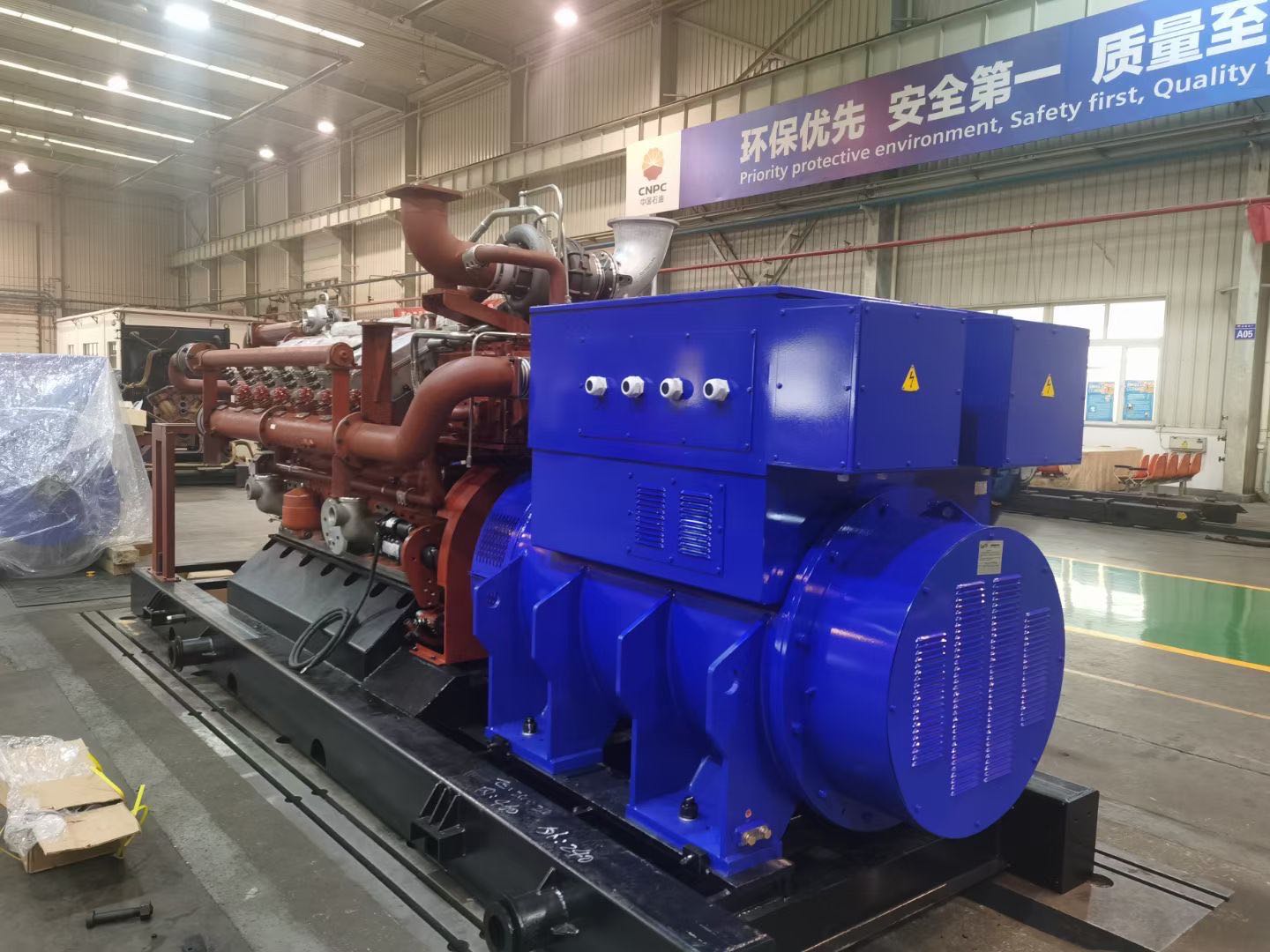
Organic silicon compounds often appear in biogas and landfill gas, and exist in the form of siloxane decomposition products, which are flammable and volatile. After combustion in the engine, this substance will produce silicon oxide, which over time will form sediment covering the surface of the engine cylinder head, which will increase the maintenance work of the engine. If the power generation system is equipped with a catalytic oxidant tail gas treatment device, such impurities can also cause catalyst failure.
Due to the volatility of volatile oxidizable silicon compounds, it is difficult to analyze their content in gas. Therefore, we can analyze the oil and, based on the testing requirements and calculation formulas provided by the generator set manufacturer, conduct two oil tests within a certain operating hour to analyze and calculate the characteristic values of the total silicon content in the oil, in order to determine whether it meets the requirements for normal operation of the unit.
Tar
If hydrocarbons in the form of solid, liquid, or high viscosity products are precipitated in the gas or mixture when cooled to below the dew point, such condensation or sublimation products are called tar. Due to different operating temperatures and thermochemical reaction processes, hundreds or thousands of different types of tar are produced during biomass pyrolysis and gasification. Usually, such hydrocarbons condense into liquid when they are cooled at low temperature, which will block the intake system, turbocharger blades, intercooler, etc.
It is difficult to completely remove tar using a simple condensation method. Therefore, for gas containing tar, it is necessary to install a heating device on the gas inlet valve group pipeline, while avoiding the mixing of low-temperature combustion air with gas containing such hydrocarbons. Analyzing the dew point of tar in biomass pyrolysis gas after pre-treatment is an effective method. The dew point of tar in gas should generally be 5 ° C or above lower than the dew point of gas, in order to prevent tar from entering components in contact with gas. Taking Yanbach gas generator unit as an example, the range of gas inlet temperature required by the unit is 10-40 ° C.
Through the above analysis, it can be found that several common impurities in gas will affect the normal operation of gas internal combustion power generation units. If gas with excessive impurities is used, in some cases, the generator unit may not immediately experience obvious problems such as operational indicator attenuation and fault shutdown. However, the harm caused by such impurities to the power generation unit will gradually accumulate, and have a very profound negative impact on the operation effect, normal maintenance clearance, and even service life of the unit.
Thank you for reading. The source of this article is: Thermal decomposition gas generator set. For more information and questions, please click on: We will continue to work hard to provide you with services. Thank you for your support!